TECHNOLOGY
Products, Technology, People
Where Evolution Meets Innovation
Innovation starts with a need. In the beginning, membrane bioreactors supported the need for better water reuse, land development, and safer effluent discharge. However, these systems, which offered advantages over CAS systems, faced operational challenges. FibrePlate™ was conceived and born to solve these challenges.
Building on 30+ years of global operational experience and lessons learned, Fibracast – pioneers of the first immersed hollow fibre (iHF) membrane systems – has once again revolutionized membrane technology with FibrePlate™, the next generation in membrane solutions.
FibrePlate™: Solving Conventional UF Membrane Challenges
FibrePlate™ overcomes key issues in traditional UF membranes, including:
- Membrane sludging
- Debris accumulation
- High OPEX costs:
- High cleaning chemical costs
- High aeration costs
- Large footprint requirements
- Low pathogen removal
FibrePlate™ Membrane
FibrePlate™ is a horizontally mounted, immersed hybrid PVDF membrane that delivers true 0.035 µm ultrafiltration through each and every module, which consists of 16 large, individual, flexible membrane sheets, functioning and operating at new enhanced levels of performance.
FibrePlate™’s performance is achieved through the fusing and integration of multiple technologies into one; hollow-fibre, flat-sheet. The net effect of this fusion is a technology greater than the sum of its parts. Conventional membranes are built with the tools and knowledge of the past.
Today, to achieve higher performance at lower costs, one has to look beyond the horizon and towards the future. FibrePlate™, the new name in Performance.
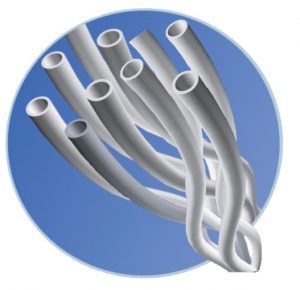
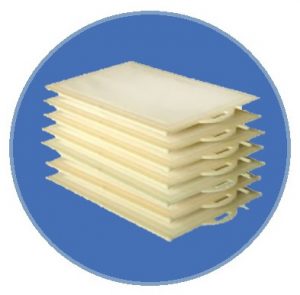
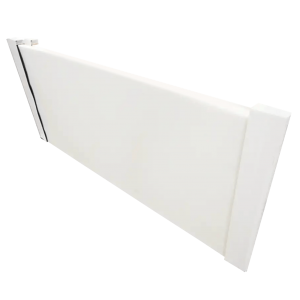
FibrePlate™ Membrane
A FibrePlate™ module consists of 16 triple-reinforced sheets, aligned horizontally, with sheet ends potted within vertical permeate collection headers. The combined surface area of the sheets delivers 500 ft² of active filtration per module.
Unlike conventional UF, membrane modules are mounted horizontally and not vertically, resulting in open free-flow passages through cassettes, reducing hydraulic restrictions and eliminating debris collection/high abrasion zones common to hollow fibre. FibrePlate™’s innovative design ensures trouble-free and simplified operations over the design life of the membrane and cassette.
FibrePlate™ Cassette
Our stainless steel cassettes are available in single, double, or triple module stacks, housing a flexible number of FibrePlate™ modules that adjust to the flow needs of your plant, allowing for the “Plug-&-Play” of modules within cassette assemblies.
Each cassette is designed as an integrated, self-supporting unit with the ability to house between 2 and 84 membrane modules. Membrane cassette configurations are flexible and allow for the use of single, double, or triple stack designs, depending on the application.
All required permeate and air connections are built into the cassette frame, reducing the number of connection points and potential leaks. As the cassette is self-supporting, its insertion and removal from a train are easily accomplished.
Membrane Train
Our membrane trains offer exceptional flexibility, with configurations that can accommodate smaller footprints or retrofit existing long membrane tank trains. The unique membrane operations and flexibility in design even allow for the retrofitting of circular clarifiers. With a broader range of configuration options, customizable train designs, and enhanced flexibility in operational control, our membrane solutions are nearly limitless, ensuring that client needs are met with the best economics, whether for greenfield projects or the retrofitting of any existing plants.
Smaller, Safer, Stronger: The Key Benefits of FibrePlate™
Unobstructed Flow Path
A primary benefit of the FibrePlate™ horizontal configuration is that there is no top header and that the modules and cassettes have an open flow configuration, with nothing to trap debris. Without restrictions or obstructions, solids go with the flow.
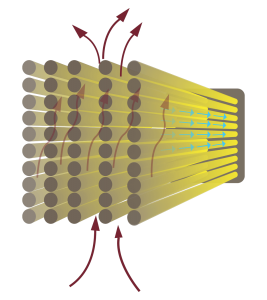
Minimized Footprint
The FibrePlate™ membrane configuration allows for a higher packing density, which translates into smaller and more optimal tank utilization compared to other types of immersed wastewater membranes.
The combination of increased packing density, improved hydraulic efficiency, and the absence of a “flow around” space between the cassettes and tank walls results in a significant footprint advantage over Plate-and-Frame and Hollow-Fiber membranes.
A smaller footprint means lower civil work costs and reduced capital costs, as the membrane tanks can be made smaller or have the capacity for future expansions.
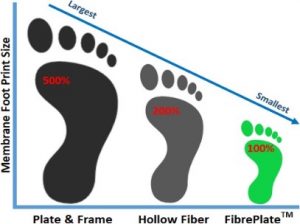
Strength and Durability
By incorporating horizontal hybrid fibers in a FibrePlate™ configuration, the stresses on the membrane are significantly reduced compared to other membrane configurations. The FibrePlate™ configuration is a self-supporting sheet that effectively transfers any shear stress away from the permeation channels and onto the potted header—a very robust membrane design.
The FibrePlate™ membrane is also extremely stable when stretched, showing minimal elongation. This eliminates the need for slack adjustment, as the membrane will not experience stretching during its lifetime, thereby reducing maintenance and downtime.
FibrePlate™ is a reinforced membrane with the ability to self-heal, as any damaged area will be quickly sealed with suspended solids. The materials used in the fabrication of the membrane are well-proven in the industry. The membrane itself is a 0.04-micron UF made from PVDF, while the reinforced sheets that support the membrane and provide structural strength are PET. The potting material is urethane.
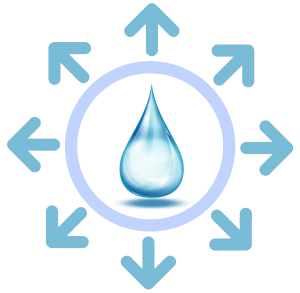
Developed and Manufactured in North America
Fibracast builds on decades of industry experience and expertise to improve upon historical membrane configurations. 100% of Fibracast membranes are manufactured in a state-of-the-art robotic facility located in Hamilton, Ontario, Canada, and shipped around the world. This local expertise and source of supply will ensure your treatment facility receives excellent service and rapid delivery of initial equipment, expansions, and spares as required.
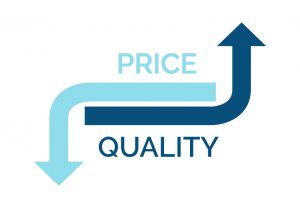
Easy Expansion
A smaller membrane footprint means that any membrane plant can increase its current flow capacity by retrofitting existing membranes with FibrePlate™. Since FibrePlate™ cassettes are designed to easily fit with the membrane trains of other manufacturers, capacity upgrades are fast and simple. Depending on the type of membranes being replaced, Fibracast can double, triple, and even quadruple plant flow.
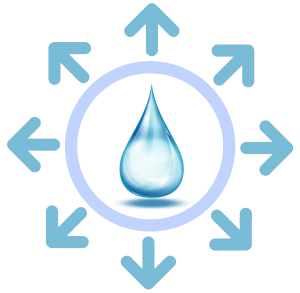
Lower Opex Costs
The FibrePlate™ membranes are the only membranes that use the combined effect of aeration and mixed liquor cross-filtration to continuously clean the membrane surfaces. This results in effective, continuous surface cleaning, which reduces the need for chemical maintenance cleans. Using the return activated sludge (RAS) flow to scour the membranes can also translate into lower energy costs, as the cost of pumping the RAS is lower than the cost of aeration.
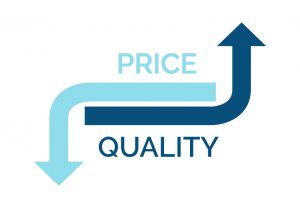
FibrePlate™ for Direct and Indirect Potable Reuse Applications
With a pore size smaller than 0.04 microns, FibrePlate™ membranes efficiently remove protozoa, bacteria, and many viral species, making them ideal for both direct and indirect potable water reuse applications.
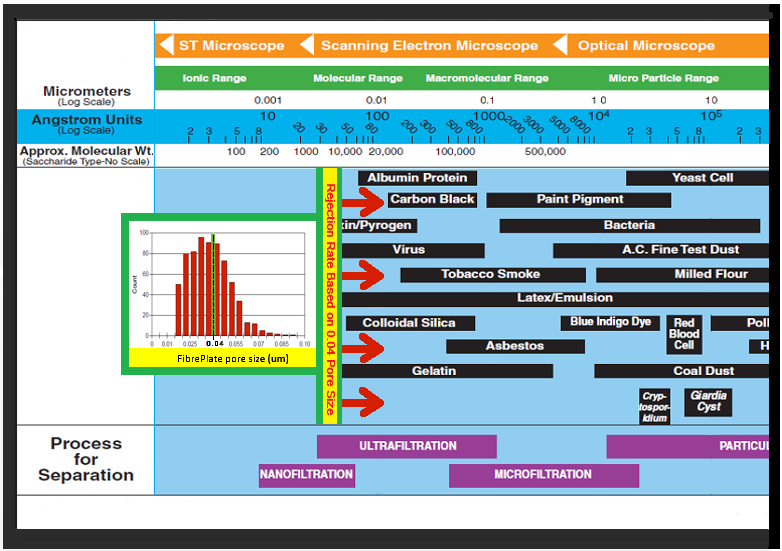